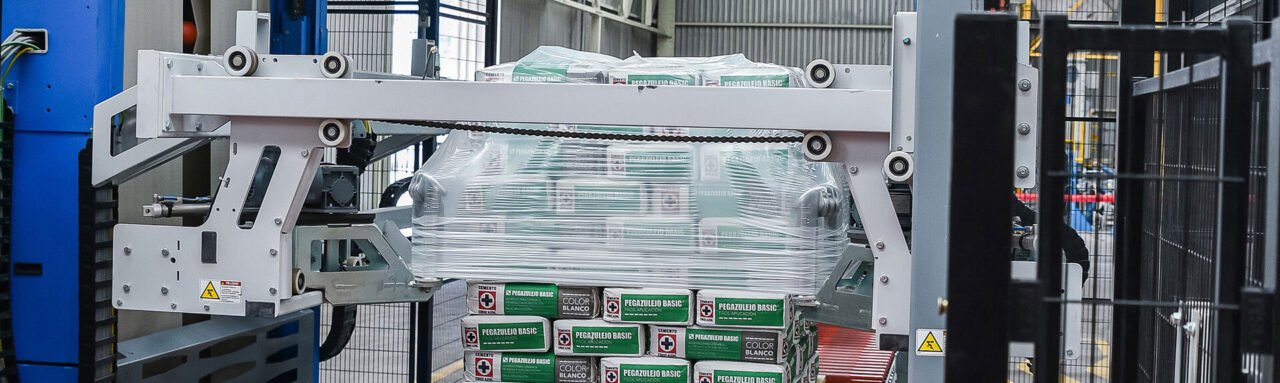
The safe, economical and sustainable transport of palletised products is an important aspect for companies. What is the good of efficiently producing goods if they only reach the customer in a damaged condition? Or if secure packaging is too cost-intensive and harmful to the environment? Three techniques have become established for the protection of your products during transport to the customer and while in storage. On this page we compare the pallet wrapper with the shrink covering and the stretch covering. We can already say that the stretch covering has proven to be very efficient compared to its competitors.
With this technique, the shrink film is pulled over the palletised goods and heated to its melting point with the help of a shrink gun. When it cools down, the film contracts and the cover size adapts to the contours of the packaged goods on the pallet. The LDPE (Low Density Polyethylene) cover shrinks to create a tension that ensures a high level of load security. This method is particularly suitable for goods which need to be handled with care during the stacking and packaging processes, such as glass. The advantages of packaging technology with PE shrink covers (polyethylene) are particularly evident in outdoor storage on Euro pallets. The covers provide protection against weather and environmental influences such as rain, snow, UV radiation, dust and insects. The disadvantage, however, is that the shrink film becomes so milky when heated, that the barcodes and products underneath cannot be easily recognised. Furthermore, the products or sacks could easily fuse together with the PE film. An increased fire risk is also a disadvantage.
The stretch wrapping method is a widely used packaging technique. Due to the comparatively low purchase price, many companies have opted for pallet wrappers. There are two types of stretch wrappers. In one technique, the pallet with the goods (e.g. cartons) sits firmly on the floor and a rotating arm moves around the packaged goods with the stretch wrap.
Other wrapping machines use a rotating turntable to rotate the pallet and the items on it. Here, the roll of film is in a fixed position. With both machines, the stretchable film is wrapped around the packaged goods on the pallet and encloses them tightly. However, the products are only fixed in the horizontal axis by the wrapping machines. The lack of a vertical fixation is a very important factor, especially during transportation. Therefore, the pallet wrapper is more suitable for comparatively light goods and not suitable for heavy and sharp-edged goods such as bricks. Furthermore, the semi-automatic film wrapper requires a considerable amount of stretch film. A frequent changing of the film roll is one of the reasons why this technology is only suitable for small quantities of goods.
Another disadvantage is the lack of film on the top of the pallet. Additional measures are therefore required to protect the goods from the elements. Due to the many layers of wrapping required, the scanning of barcodes is a problem and the display effect is also far from optimal plus the surface cannot be printed on. Due to the adhesive effect of the stretch film dust particles and dirt are also attracted to it, especially during prolonged storage. Due to the unwrapped upper end, unauthorised persons can quite easily remove goods without damaging the packing material. It is quite common for the film end to detach itself from the pallet and stick out slightly, thus interfering with the sensory system of the conveying technology in warehouses. Accidents have already occurred when handling the pallets due to the protruding stretch film getting caught on shelving systems.
The stretch cover was developed from a combination of the pallet wrapper and shrink cover. The flexible stretch film used here adapts to the goods as with the film wrapper, but heating is not necessary. This considerably increases operational safety and fire protection. How does the process work? The stretch cover is made of LDPE (Low Density Polyethylene). It is stretched by the packaging machine and pulled over the palletised goods fully automatically from above. The tubular film contracts again immediately after being pulled over the pallet and ensures increased load stability without sticking to the product. This process offers many advantages. The cover is very transparent and therefore has a very good display effect in the sales area and barcodes underneath can be read without any problems. Sustainability is an increasingly important issue. The pallet cover used is recyclable and needs less and thinner material than the previously discussed procedures. The packaging for transport is done in a single layer and is accurate to the centimetre due to its fully automatic pallet recognition function. This means that only the length of film that is actually required is used. Consequently, by using less Film material and energy there is less of an impact on the environment. Even when stored outside, the securely packed goods are resistant to all weather conditions. The packaged goods are effectively protected from six sides by an additional layer of film.
High load stability
Excellent display qualities
Protection against environmental impacts and interference
Low power and film use
Fully automatic pallet and package recognition
Film length automatically calculated using ultrasound
Customer Support proativo para a sua indústria
Nosso suporte vai além do padrão – é uma parceria feita para durar. Com o apoio de uma rede mundial de centros de serviços regionais, estamos com você durante todo o ciclo de vida dos seus sistemas e instalações, entendendo suas necessidades exclusivas para garantir o máximo de confiabilidade e eficiência.
Trabalhamos 24 horas por dia, 7 dias por semana, para sermos o seu Partner of Choice.